Gearbox Whine? Solving Common Failures Caused by Inadequate Lubrication
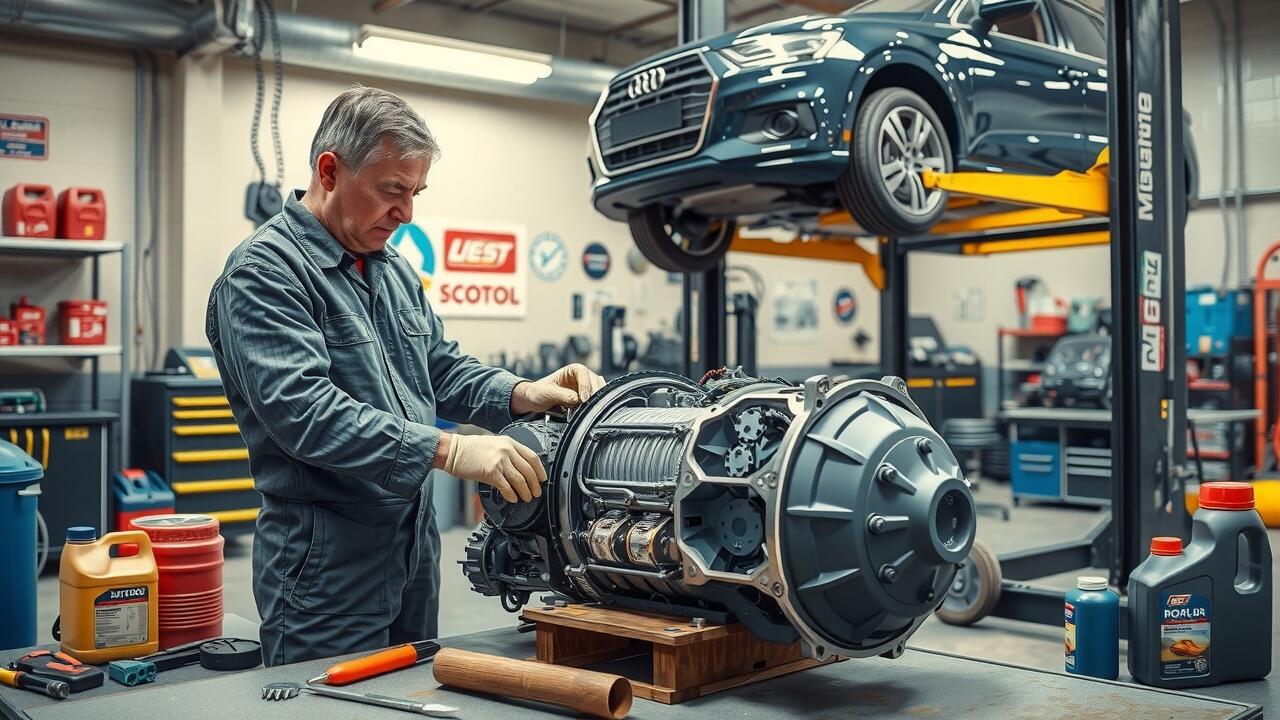
Key Takeaways
- Consistent upkeep enhances gearbox performance.
- Identifying the optimal timing for oil changes.
- Methodical process for diagnosing gearbox noise.
- Influence of design on lubrication effectiveness.
- Selecting appropriate oil for gearbox needs.
How Can Regular Maintenance Improve Gearbox Functionality?
Regular maintenance plays a crucial role in enhancing gearbox functionality and longevity. Implementing a routine that includes checking and replacing gear oil ensures optimal performance. For example, adhering to the manufacturer's recommendations, such as changing the gearbox oil every 5,000 to 10,000 operating hours, can significantly reduce the likelihood of wear and catastrophic failures. Scheduled inspections allow for the identification of leaks or seal degradation, enabling timely repairs that prevent larger, costlier issues down the road.
Employing systematic checks enhances lubrication effectiveness. Proper gear lubrication facilitates consistent operation by minimizing friction and heat buildup within the gearbox. Not just checking oil levels, but assessing oil condition, including viscosity and contamination levels, provides insights into the system’s health. Research indicates that effective gearbox lubrication reduces operating temperatures by up to 30%, thereby extending service intervals. Investing in quality gear box oil not only promotes efficiency but also aligns with industry best practices, ensuring compliance with operational standards and regulatory requirements.
The Role of Scheduled Inspections in Preventing Failures (Creating maintenance routines and checking seals)
Scheduled inspections serve as a crucial component in maintaining the integrity of gearbox functionality. Implementing a routine that involves regular checks can significantly increase the lifespan of gearboxes. For example, a study conducted by an industry leader in gearbox technology revealed that companies performing bi-annual inspections experienced a 40% reduction in equipment failure rates compared to those that neglected regular maintenance. During these inspections, personnel should focus on assessing the integrity of seals, as compromised seals can lead to the loss of gear oil, ultimately affecting gearbox lubrication and performance.
Additionally, maintaining a detailed log of inspection findings facilitates the identification of recurring issues. Technicians can track changes over time, revealing patterns that suggest underlying problems. For instance, discrepancies in oil viscosity or color during inspections can indicate not just the need for oil change but also point toward more significant mechanical issues. By addressing these conditions swiftly, organizations can prevent costly downtime and extend the operational efficiency of their gearboxes, leveraging best practices in lubrication management to avoid severe mechanical failures in the long run.
When to Replace Gearbox Oil
Routine monitoring of gear oil conditions can reveal the need for replacement before significant degradation occurs. A common guideline within the industry is to change gearbox oil every 1,000 to 2,000 operating hours, depending on the specific application and operating environment. For instance, in high-load or high-temperature applications, more frequent changes might be necessary. Regular sampling and analysis of the lubricant can also provide insights into the oil's condition, offering a proactive approach to maintenance that aligns with industry best practices.
Signs indicating that gearbox lubrication may require replacement include noticeable color changes, the presence of debris, or unusual odors emanating from the oil. Typically, healthy gear oil appears clear or slightly dark depending on the type of lubricant used. However, if the oil turns a milky color, this could indicate contamination from water. Substantial debris signifies wear, which could lead to further component damage if not addressed immediately. Regular checks for these indicators not only extend the lifespan of your gearbox but also reduce operational downtime and maintenance costs through timely interventions.
Signs Indicating Oil Change is Necessary (Color change, unusual odor, and debris presence)
Monitoring the color of gearbox oil is a crucial step in maintenance routines. In healthy oil, a clear, amber hue typically signifies that lubrication remains effective. Conversely, a dark or milky appearance often indicates contamination with water or microscopic debris. For instance, oil that becomes excessively dark could signal oxidation or thermal breakdown, reducing its ability to protect gearbox components. Regular visual inspections can help identify these color variations promptly, enabling timely interventions to prevent extensive damage.
Unusual odors emitted from the gear oil can also serve as warning signs. A burnt smell might suggest overheating or the presence of contaminants, while a sour or rancid odor could imply chemical degradation of the lubrication properties. Moreover, debris presence, including metal shavings or grime, often indicates excessive wear within the gearbox. An oil analysis can quantify such particulates, providing data for maintenance decisions. Adhering to industry standards for oil changes can enhance gearbox lubrication, ensuring optimal performance during operation.
Troubleshooting Gearbox Whine
Addressing gearbox whine begins with a systematic diagnosis of lubrication-related issues. Utilizing oil analysis can provide insights into the performance of gear oil within the system. This analysis can reveal the presence of metal shavings or contaminants that may indicate wear. Additionally, a detailed visual inspection of seals can help identify any leaks that may compromise gearbox lubrication, leading to inadequate oil levels and increased noise levels. Maintenance records should also be reviewed to determine the consistency of oil changes. Ideally, following the manufacturer's recommendations, intervals for oil changes should not exceed six months or 1,000 operating hours, whichever comes first.
Noise checks during operational status are crucial for pinpointing the root cause of whine. By employing sound frequency analysis, technicians can detect anomalies that may correlate with insufficient lubrication or improper oil distribution. If the noise correlates with a specific load or speed, further investigation into bearing conditions is warranted. For instance, altered gear alignment can cause uneven wear, amplifying whining sounds. Ensuring that components are correctly aligned and that sufficient gearbox lubrication is maintained may not only mitigate noise but also enhance overall operational efficiency.
Diagnosing Common Issues Related to Lubrication (Visual inspections, oil analysis, and noise checks)
Conducting visual inspections is crucial for diagnosing lubrication issues in gearboxes. Technicians should examine seals, housing, and breather vents for signs of wear, leaks, or contamination. For instance, a common indication of insufficient gear oil is the presence of residue around seals, which can lead to further lubrication failures if not addressed promptly. Regular assessments should occur on a schedule, ideally every 1,000 operating hours, to maintain optimal gearbox performance.
Oil analysis serves as a powerful diagnostic tool for evaluating the condition of gearbox lubrication. Samples taken from the oil can reveal critical contaminants such as metal particles or excessive moisture, both of which signal underlying mechanical wear or compromised sealing. Industry standards recommend conducting oil analysis at least twice a year or more frequently for high-load applications. Noise checks are also beneficial in this context; abnormal sounds, such as whining or grinding, often indicate inadequate oil levels or distribution issues, necessitating immediate action. Regular monitoring not only aids in troubleshooting but also helps prevent potential catastrophic failures.
The Impact of Gearbox Design on Lubrication Efficiency
Gearbox design significantly influences lubrication efficiency and overall performance. For instance, specific gearbox architectures, such as helical or bevel gears, create distinct lubrication pathways that affect the flow of gear oil. Proper alignment of bearings within these designs establishes optimal channels for oil distribution, which is essential for minimizing friction and preventing overheating. Insufficient lubrication can lead to wear rates exceeding acceptable thresholds, with studies indicating that improper gear oil application can increase bearing failure rates by up to 50%.
Additionally, the material composition and surface finish of gearbox components are crucial in determining lubrication effectiveness. For example, gears made from high-strength alloys may require specialized formulations of gearbox lubrication to maintain viscosity and prevent degradation under high stress. Implementing best practices, such as routine oil sampling and viscosity checks, ensures that the lubricant maintains its protective properties. Regular assessments can help identify potential issues before they escalate, leading to improved longevity and reliability of gearbox systems.
How Gear Design Affects Oil Flow and Distribution (Understanding lubrication pathways and bearing placements)
The design of a gearbox plays a critical role in its lubrication efficiency. Geometry and layout determine how effectively the gear oil can flow throughout the unit. For instance, improperly placed bearings can lead to oil starvation in high-friction areas, raising the risk of component wear and failure. A study from the American Gear Manufacturers Association emphasizes that optimal bearing placement and well-engineered lubrication pathways enhance the flow of gearbox lubrication, ultimately resulting in an extended service life.
Analyses of gearbox designs have revealed that specific configurations yield varying degrees of oil distribution efficiency. For example, helical gears typically offer better oil flow compared to spur gears due to their angled teeth. This geometry allows for superior engagement and reduces the likelihood of localized high-pressure zones where lubrication becomes insufficient. Professionals in the field recommend adhering to the American Society of Mechanical Engineers’ (ASME) standards for gearbox lubrication to maximize performance. Regular assessments and a proactive maintenance strategy ensure that gear box oil operates under ideal conditions, mitigating unnecessary wear and tear.
Choosing the Right Gearbox Oil
Selecting the appropriate gear oil is crucial for maximizing gearbox performance and longevity. Various formulations are available, ranging from synthetic to mineral-based oils, each designed to meet specific operational conditions. For instance, synthetic oils often exhibit superior viscosity stability and lower temperature operating ranges compared to their mineral counterparts, making them ideal for high-stress environments. According to industry standards, such as ISO 12925 or AGMA 9005, the right viscosity grade and additives can significantly minimize wear and enhance gearbox lubrication effectiveness, ultimately improving efficiency and reducing downtime.
When evaluating gearbox oil, professionals should consider factors governing the selection process. These include the gearbox design, load conditions, and operating temperature. For example, in high-load applications, a high-viscosity gear oil with EP (Extreme Pressure) additives may be essential to protect against surface degradation. Implementing regular analysis of the lubricant allows for proactive maintenance; monitoring color changes, contamination levels, and viscosity can provide insights into the condition of both the oil and the gearbox. With these measures in place, operators can significantly decrease the risk of failures and extend the service life of their gearboxes.
FAQS
What causes gearbox whine?
Gearbox whine is often caused by inadequate lubrication, which can lead to increased friction and wear on the gears. Other factors may include improper gear alignment and the presence of contaminants in the oil.
How often should I perform maintenance on my gearbox?
Regular maintenance should be performed according to the manufacturer’s recommendations, typically every 6 to 12 months. This includes scheduled inspections and oil changes to ensure optimal functionality.
What are the signs that indicate it’s time to replace gearbox oil?
Signs that it’s time to replace gearbox oil include a noticeable color change, an unusual odor, and the presence of debris in the oil. If you observe any of these symptoms, it’s essential to conduct an oil change promptly.
How can I troubleshoot gearbox whine effectively?
To troubleshoot gearbox whine, start with visual inspections to check for signs of wear. Conduct an oil analysis to assess the condition of the lubricant, and perform noise checks to identify the source of the whine.
Does gearbox design influence lubrication efficiency?
Yes, gearbox design significantly impacts lubrication efficiency. The configuration of lubrication pathways and the placement of bearings can affect oil flow and distribution, which are crucial for maintaining proper lubrication levels.